Concept & Design
Concept & Design
Our expertise begins at the conceptual stage where we assist clients in refining their product ideas, ensuring manufacturability, and optimizing performance. We use cutting-edge software for 3D modeling, prototyping, and design validation, allowing for rapid iteration and development.
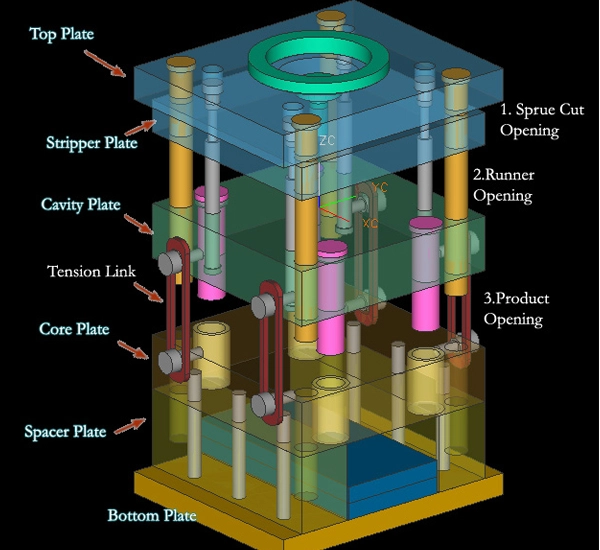
Engineering & Design Capabilities
- DFM (Design for Manufacturability): Ensuring designs are optimized for efficient production while minimizing costs.
- Material Selection: Expertise in choosing the right thermoplastics for durability, strength, and environmental factors.
- Tooling & Mold Design: Precision mold development using advanced CAD/CAM technology.
- Rapid Prototyping: 3D printing and test molding for early-stage evaluations.
- Mold Flow Analysis (MFA): Simulates stress and performance to catch issues early.